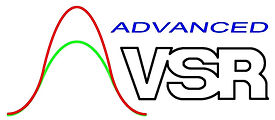
It is hard to find a milling machine worth anything these days, that does not have a brushless motor in its spindle. Brushless motor technology has also revolutionized other industries, from electric cars and trains to hand power tools.
We are the only builder of vibratory stress relief equipment in North America that uses brushless motors, which we use exclusively. Why use anything else ?
Learn more on our Equipment Comparison page.

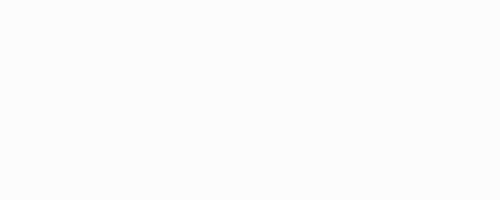
WE INVENTED THE VSR PROCESS
VIBRATORY STRESS RELIEF EQUIPMENT
Three models . . . all user friendly

Our basic system's features :
3 kW Allen-Bradley motor drive with external heat sink (80% heat dissipation is outside the NEMA 4-grade enclosure)
Digital displays of workpiece vibration amplitude, vibrator motor current, vibrator speed / RPM
Digital speed control increment of 6 RPM
300 - 7500 RPM 3 phase motor with 20:1 adjustable unbalance.
Our popular mid-priced system's distinguishing features :
3 kW Allen-Bradley motor drive with external heat sink (80% heat dissipation is outside the NEMA 4-grade enclosure)
CNC control, via a 15” industrial touchscreen. The PC is “fanless” (runs cool / no fan needed) and has a solid state HD. Nothing mechanical on its die-cast aluminum chassis, for maxium ruggedness and reliability. VSR Treatments saved by printing as PDF (PDF maker installed at factory).
VSR Chart data includes plot of both workpiece amplitude AND motor power vs. vibrator RPM, the most useful data for the operator to fine-tune VSR Setups and process your parts quickly.
300 – 9000 RPM speed range vibrator, that develops a max 3200 lbs of force. Adjustable (takes 1 minute) unbalance over a 20:1 range allows wide range of workpieces to be VSR Processed with this system.
Speed regulation of less than 0.1% and adjustable frequency increment of 6 RPM.
Shown with mobile workstation with NEMA 4 enclosed disconnect switch, circuit breaker and 3 kVA isolation transformer.
The Model 8a is the STATE-OF-THE-ART VSR System:
This system was used to stress relieve the massive, 177 ton storm-surge gates for the City of New Orleans.
5 kW Allen-Bradley motor drive with external heat sink (80% heat dissipation is outside the NEMA 4-grade enclosure)
CNC control, via a 15” industrial touchscreen. The PC is “fanless” (runs cool / no fan needed) and has a solid state HD. Nothing mechanical on its die-cast aluminum chassis, for maxium ruggedness and reliability. VSR Treatments saved by printing as PDF (PDF maker installed at factory).
VSR Chart data includes plot of both workpiece amplitude AND motor power vs. vibrator RPM, the most useful data for the operator to fine-tune VSR Setups and process your parts quickly.
Dual flanged 100 – 8000 RPM speed range vibrator, that develops a max 7500 lbs of force, can be used in any orientation, including shaft vertical. Large rings, such as those common to the hydroturbine industry, require treatment with shaft vertical. The perpendicular flanges make it easy for an operator to orient the vibrator properly, relative to the workpiece.
Adjustable (takes 1 minute) unbalance over a 20:1 range allows wide range of workpieces to be VSR Processed with this system.
Speed regulation of less than 0.02% and fine tuning increment of 2 RPM.
Shown with mobile workstation with NEMA 4 enclosed disconnect switch / circuit breaker package and 3 kVA isolation transformer.
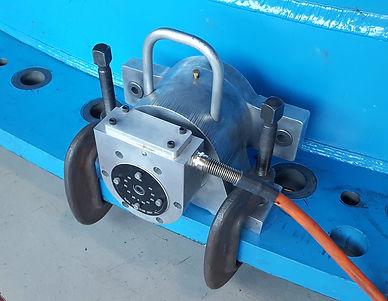
ADVANCED VSR STRESS RELIEF SYSTEMS HAVE SEVERAL UNIVERSAL FEATURES MAKING THEM THE BEST VALUE ON THE MARKET:
- CNC Models contain Advanced VSR's 5.3.1 Software, which automatically performs one of the toughest tasks in performing the VSR Process: Recording and plotting the workpiece resonance pattern. Using this software, the operator can easily generate preliminary scans used to evaluate and adjust the initial VSR Setup, record base-line resonance patterns, and then easily tune the vibrator upon resonances of the workpiece, while watching them grow, shift or both, to their final, stable positions. These steps together are what is called, the VSR PROCESS.
- NEMA 4 - grade enclosures prevent dust, dirt, debris, oil or spraying water from entering, greatly extending electrical and electronic component life.
- BRUSHLESS AC induction or AC sync motors. Carbon brushes produce highly conductive dust (esp. if the motor is undergoing vibration), coating the motor's interior, leading to faults and frequent equipment failure. Brushes also limit the speed range of the motor. We highly recommend avoiding equipment that uses any form of vibrator with carbon brushes.
- Thermal sensors embedded in the motor windings supply signals that shutoff the motor drive, if over-temperature occurs. With the CNC controlled models (7.5 and 8a) the motor temperature is displayed on the VSR OS, alerting the operator before an over-temperature event occurs, promoting best practice operation.
- Allen-Bradley AC motor drives, considered by many the "gold-standard" of VFD's have external heat sinks, which dissipate more than 80% of the drive's heat directly outside the console, reducing temperatures inside the console which greatly extends component and wiring lifetime.
- Max rugged and reliability components, from vibrator connectors with die-cast aluminum housings to pushbuttons with gold-flashed contacts, these systems have been designed and built to standards used in the highest quality machine tools and industrial control panels, which our panel shop also builds for numerous industries, including electric utilities.
- All vibrators have hardened steel inserts in their mounting feet, allowing secure, non-degrading clamping quality, which assures both clean vibration data and minimal long-term wear.
- All systems include urethane isolation cushions, machinist / bridge vibrator clamps, a low-noise pre-amplified accelerometer with fully balanced and shielded line output, all connecting cables, comprehensive manual supplied in plastic sheet protected 3 ring binder (survives shop use, also supplied electronically), and a 2 year parts and labor factory warranty.